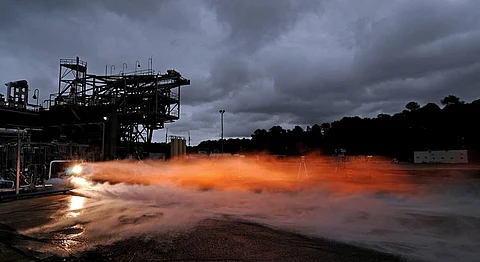
3-D printing, or additive manufacturing by its proper terminology, has taken the world by storm. People around the world have used it to create all sorts of things in the avenues of education, art, medicine, space, weaponry, entertainment and numerous others. 3-D printers have built houses, created low-cost prosthetics; recently, using a 3-D bio-printer three scientists in Bangalore developed tissues with the ability to perform functions of the human liver. The potential that a 3-D printer has is gradually being recognised and it has become one of the most propitious technologies that can create pretty much anything under the Sun.
With the aim in mind to create a working high-performance 3-D printed rocket engine, for the past three years the NASA team at the Marshall Space Flight Center in Huntsville, Alabama, has been working with a number of vendors and printed parts of a rocket engine -- turbo-pumps, injectors and valves --each tested individually with fruitful results. In their latest test late last year, the Marshall team tested these pieces together with cryogenic liquid hydrogen and oxygen, placing them to work as they would in a real engine and the result was a fiery spew of more than 20,000 pounds of thrust, and able to survive temperatures of 6,000 degrees Fahrenheit, approximately 3,315 degrees Celsius. "We manufactured and then tested about 75 percent of the parts needed to build a 3-D printed rocket engine," said Elizabeth Robertson, the project manager for the additively manufactured demonstrator engine in a release posted by NASA. "By testing the turbo-pumps, injectors and valves together, we've shown that it would be possible to build a 3-D printed engine for multiple purposes such as landers, in-space propulsion or rocket engine upper stages."
The thunderous video NASA posted of the rocket firing along with the release shows incredible progress towards their goal. This ‘breadboard engine’ of various parts strung together may not exactly look like a traditionally manufactured rocket engine, which itself raises initial doubts regarding the reliability of printed materials. "What matters is that the parts work the same way as they do in a conventional engine and perform under the extreme temperatures and pressures found inside a rocket engine,” explains Nick Case, lead on the testing efforts in the release, shutting down these doubts. He adds further: “The turbopump got its "heartbeat" racing at more than 90,000 revolutions per minute (rpm) and the end result is the flame you see coming out of the thrust chamber to produce over 20,000 pounds of thrust, and an engine like this could produce enough power for an upper stage of a rocket or a Mars lander."
A rocket engine has incredibly complex components that need to be made with incredible precision in specific shapes to withstand the high pressures and speeds. 3-D printing has proven to be very advantageous in this aspect as parts can be designed down to each detail and entered into the printers computer. The printer then builds each part by layering metal powder and fusing it together with a laser – a process known as selective laser melting. The 3-D printed parts can be made without need of welds or joins, and even be altered or enhanced in design for optimal aerodynamics or fuel-flow. The total number of components have reduced as parts are being built as single items, a feat which engineers had previously been unable to do. For example, a traditionally manufactured injector has more than 200 parts, compared to this, the 3-D printed one has just two, also incorporating features that haven’t been used before and became possible only with additive manufacturing; time taken for manufacturing has drastically decreased as well, parts that would take years to be traditionally built can now be produced in a matter of months -- valves took a few months to be made whereas normally it would take more than a year. “This new manufacturing process really opened the design space and allowed for part geometries that would be impossible with traditional machining or casting methods,” said David Eddleman, one Marshall’s propulsion designers. “For the valve designs on this engine, we used more efficient structures in the piece parts that resulted in optimized performance.”
The benefit of cutting costs and time that 3-D printing allows has gained importance, making it possible to have parts built and assembled, ready on the test stand a lot sooner than would be had they been possible had they been obtained through traditional manufacturing methods. The major concern that surrounds the debate regarding the use of 3-d printers in such an important and major industry is the reliability of the printed material that are suspected to be a lot more delicate and non-durable than their traditional counterparts. But as we see in the tests video posted by NASA, these printed parts are able to stand their ground unfaltering in highly hostile conditions, the same environmental stressors of a real rocket launch.
“The advances in the technology are finally getting to the point where we can see parts additively manufactured for demanding NASA applications,” Dale Thomas, associate technical director at the Marshall Space Flight Center, told Fortune. “We’re never going to get away from the traditional manufacturing process. But additive is going to have some real game-changing benefits.” Additive manufacturing as proven itself to be a serious game-changer for space technology and has opened up opportunities for new missions, both in space and on Earth. Future plans, as stated by team, include performing tests of the engine with liquid oxygen and methane -- -key propellants for Martian landers since methane and oxygen production might be possible on the ‘Red Planet’ Mars. Slowly but surely, NASA moves step by step closer to their goal and a fully-functional 3-D printed rocket, and who knows what else, may be launched into space sooner than you think, and we could not be more excited.
Watch the rocket engine come to life in the video posted below. NASA has uploaded a series of videos of their tests to Youtube and the official website.
NASA engineer Nick Case talks about the breadboard engine and explains how engineers configured engine parts to make and test 3-D printed engine parts as a system in the NASA video posted below.
Words: Sara Hussain